Bí quyết cải tiến liên tục – Chìa khóa để thành công bền vững
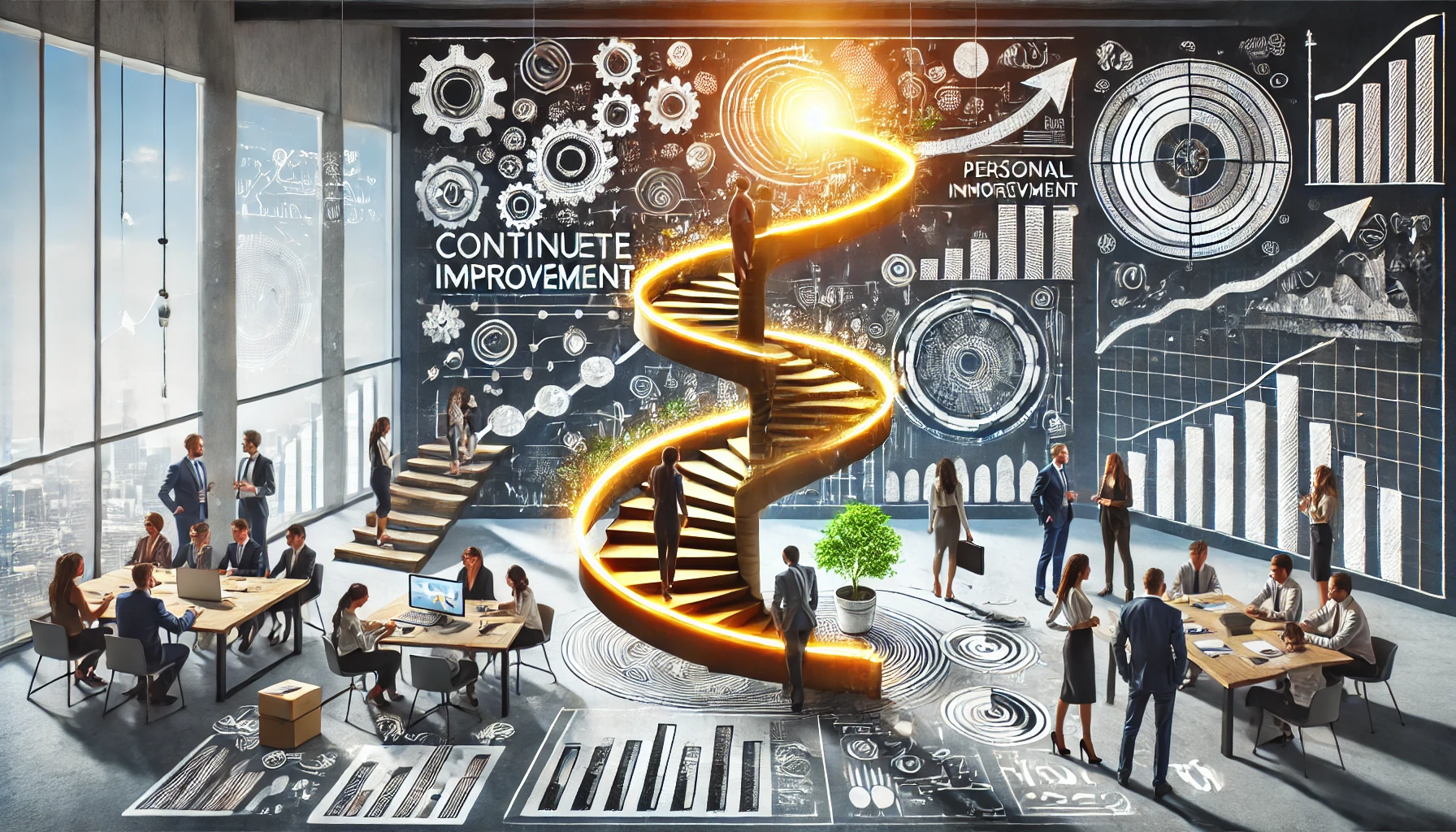
Tóm tắt
Cải tiến liên tục không chỉ đơn thuần là một phương pháp quản lý hay một chiến lược kinh doanh, mà còn là một triết lý giúp cá nhân và tổ chức duy trì sự phát triển bền vững trong một thế giới không ngừng thay đổi. Những doanh nghiệp và cá nhân thành công nhất không phải là những người mạnh nhất hay có nguồn lực dồi dào nhất, mà là những người biết cách thích nghi, đổi mới và tối ưu hóa liên tục.
Như Benjamin Franklin từng nói:
“Without continual growth and progress, such words as improvement, achievement, and success have no meaning.”
(Không có sự phát triển liên tục, những từ như cải tiến, thành tựu và thành công sẽ không có ý nghĩa) [1].
Trong kỷ nguyên số, nơi mà công nghệ, thị trường và nhu cầu khách hàng thay đổi nhanh chóng, việc duy trì một tư duy cải tiến liên tục giúp các tổ chức không chỉ sống sót mà còn vươn lên dẫn đầu. Những doanh nghiệp như Toyota, Amazon hay Google đã chứng minh rằng cải tiến không phải là một dự án nhất thời, mà là một quá trình dài hạn mang tính chiến lược.
Bài viết này sẽ đi sâu vào những công cụ và phương pháp giúp cá nhân và tổ chức triển khai cải tiến liên tục một cách hiệu quả. Từ PDCA (Chu trình Lập kế hoạch – Thực hiện – Kiểm tra – Hành động), Kanban (Quản lý luồng công việc), 5S (Tổ chức nơi làm việc), đến Lean Manufacturing (Tối ưu hóa quy trình sản xuất), tất cả đều là những công cụ quan trọng giúp tối ưu hóa hiệu suất, loại bỏ lãng phí và tạo ra giá trị bền vững.
Câu hỏi đặt ra là: Làm thế nào để áp dụng tư duy cải tiến liên tục một cách hiệu quả? Những công cụ nào phù hợp nhất cho từng mô hình kinh doanh và từng lĩnh vực cụ thể? Bài viết này sẽ cung cấp câu trả lời chi tiết và hướng dẫn thực tế để giúp bạn áp dụng ngay vào công việc và cuộc sống.
I. Giới thiệu
Trong môi trường kinh doanh hiện đại, không có điều gì chắc chắn ngoài sự thay đổi. Một sản phẩm có thể là tiên phong hôm nay, nhưng có thể trở nên lỗi thời chỉ sau vài tháng nếu không được cải tiến. Một quy trình hiệu quả hiện tại có thể không còn phù hợp khi thị trường và công nghệ thay đổi. Điều này khiến cải tiến liên tục trở thành yếu tố sống còn, không chỉ dành cho doanh nghiệp mà còn cho từng cá nhân.
Như Charles Darwin đã từng nhấn mạnh:
“It is not the strongest of the species that survive, nor the most intelligent, but the one most responsive to change.”
(Không phải loài mạnh nhất hay thông minh nhất tồn tại, mà là loài biết thích nghi tốt nhất với sự thay đổi) [2].
Điều này đúng với mọi khía cạnh của cuộc sống và kinh doanh. Một công ty có thể có nguồn lực dồi dào, đội ngũ xuất sắc và sản phẩm tuyệt vời, nhưng nếu không đổi mới và cải tiến liên tục, nó sẽ dần bị bỏ lại phía sau. Kodak, Nokia hay BlackBerry là những ví dụ điển hình về việc không kịp thích nghi và cải tiến, dẫn đến việc đánh mất thị phần vào tay các đối thủ linh hoạt hơn.
Tuy nhiên, cải tiến liên tục không chỉ là việc áp dụng công nghệ mới hay thay đổi quy trình. Đó là một triết lý quản lý bao gồm nhiều yếu tố:
- Tối ưu hóa hiệu suất cá nhân và tổ chức – Không ngừng tìm kiếm cách làm việc hiệu quả hơn, thông minh hơn.
- Giảm thiểu lãng phí – Loại bỏ những quy trình không tạo ra giá trị, giúp doanh nghiệp tiết kiệm chi phí và nâng cao chất lượng sản phẩm/dịch vụ.
- Xây dựng văn hóa học hỏi – Khuyến khích nhân viên chủ động đề xuất sáng kiến, thử nghiệm ý tưởng mới và liên tục phát triển kỹ năng.
- Duy trì lợi thế cạnh tranh – Doanh nghiệp nào có khả năng cải tiến nhanh hơn sẽ chiếm lĩnh thị trường và giữ vững vị thế dẫn đầu.
Ví dụ điển hình là Toyota với triết lý Kaizen – nghĩa là “cải tiến liên tục” trong tiếng Nhật. Công ty này không ngừng điều chỉnh, tối ưu hóa quy trình sản xuất, giúp họ duy trì chất lượng hàng đầu trong ngành công nghiệp ô tô. Amazon cũng là một minh chứng tiêu biểu khi liên tục cải tiến mô hình vận hành, giao hàng nhanh hơn, tối ưu hóa trải nghiệm khách hàng và mở rộng quy mô với tốc độ đáng kinh ngạc.
Vậy làm thế nào để áp dụng cải tiến liên tục vào thực tế?
Bài viết này sẽ cung cấp một hướng dẫn chi tiết về các công cụ quan trọng như PDCA, Kanban, 5S, Lean Manufacturing, giúp bạn hiểu rõ cách áp dụng để nâng cao năng suất cá nhân và tổ chức. Dù bạn là một nhà lãnh đạo doanh nghiệp, một chuyên gia trong ngành hay một cá nhân muốn phát triển bản thân, việc hiểu và ứng dụng cải tiến liên tục sẽ giúp bạn đạt được những thành công bền vững.
II. Nội dung
1. PDCA – Chu trình Lập kế hoạch, Thực hiện, Kiểm tra, Hành động
PDCA (Plan – Do – Check – Act) không chỉ là một công cụ quản lý chất lượng đơn thuần mà còn là triết lý giúp duy trì và thúc đẩy cải tiến liên tục (Continuous Improvement) trong mọi lĩnh vực. Chu trình này được phát triển bởi Tiến sĩ W. Edwards Deming, người được coi là cha đẻ của quản lý chất lượng hiện đại, và được áp dụng rộng rãi trong sản xuất, dịch vụ, quản lý dự án và phát triển tổ chức.
Như John Ruskin đã từng khẳng định:
“Quality is never an accident; it is always the result of intelligent effort.”
(Chất lượng không bao giờ là ngẫu nhiên, nó luôn là kết quả của nỗ lực thông minh) [3].
Cấu trúc của PDCA
- Plan (Lập kế hoạch):
- Xác định vấn đề hoặc cơ hội cải tiến.
- Thu thập dữ liệu và phân tích nguyên nhân gốc rễ.
- Đề xuất các giải pháp khả thi và xây dựng kế hoạch hành động.
- Xác định các tiêu chí đánh giá kết quả.
- Do (Thực hiện):
- Triển khai thử nghiệm trên quy mô nhỏ để giảm thiểu rủi ro.
- Ghi nhận dữ liệu thực tế và phản hồi trong quá trình triển khai.
- Đảm bảo rằng các nhân viên hoặc đội nhóm liên quan hiểu rõ kế hoạch và có đủ nguồn lực thực hiện.
- Check (Kiểm tra):
- Đo lường kết quả so với mục tiêu ban đầu.
- Phân tích dữ liệu để xác định xem giải pháp có hiệu quả không.
- Xác định những điểm cần cải tiến trước khi mở rộng quy mô.
- Act (Hành động):
- Nếu thử nghiệm thành công, mở rộng quy mô triển khai.
- Nếu kết quả chưa đạt mong đợi, quay lại bước Plan để điều chỉnh và tiếp tục thử nghiệm.
- Tạo tài liệu và chuẩn hóa quy trình để đảm bảo cải tiến được duy trì lâu dài.
Ứng dụng của PDCA
PDCA có thể áp dụng trong nhiều lĩnh vực khác nhau:
- Quản lý sản xuất: Kiểm soát chất lượng, giảm thiểu lãng phí, tối ưu hóa dây chuyền sản xuất.
- Quản lý dự án: Xác định rủi ro, đánh giá tiến độ, cải tiến hiệu suất đội nhóm.
- Dịch vụ khách hàng: Cải thiện quy trình phản hồi khách hàng, nâng cao trải nghiệm người dùng.
- Công nghệ thông tin: Phát triển phần mềm theo phương pháp Agile, liên tục tinh chỉnh sản phẩm.
- Phát triển cá nhân: Tự đánh giá kỹ năng, đặt mục tiêu học tập và cải thiện hiệu suất làm việc.
Ví dụ thực tế về PDCA
Toyota – Công ty tiên phong trong cải tiến liên tục
Toyota là một trong những tập đoàn áp dụng PDCA thành công nhất trong hệ thống Toyota Production System (TPS). Khi phát hiện một lỗi nhỏ trong dây chuyền sản xuất, họ ngay lập tức dừng lại để điều tra vấn đề, sau đó thực hiện thử nghiệm cải tiến trên một khu vực nhỏ trước khi áp dụng trên toàn hệ thống. Điều này giúp Toyota duy trì tiêu chuẩn chất lượng cao và giảm thiểu sai sót ngay từ giai đoạn đầu.
Amazon – Nâng cao trải nghiệm khách hàng
Amazon không ngừng sử dụng PDCA để tối ưu hóa trải nghiệm mua sắm trực tuyến. Họ liên tục thu thập dữ liệu về hành vi khách hàng (Plan), thử nghiệm giao diện hoặc tính năng mới (Do), đo lường mức độ hài lòng của khách hàng (Check), và nếu cải tiến có hiệu quả, họ sẽ triển khai rộng rãi (Act).
Tại sao PDCA hiệu quả?
- Giúp tổ chức trở nên linh hoạt hơn: Thay vì triển khai thay đổi một cách vội vàng, PDCA cho phép doanh nghiệp kiểm tra hiệu quả của từng bước nhỏ trước khi mở rộng quy mô.
- Giảm thiểu rủi ro và chi phí: Thử nghiệm trên quy mô nhỏ giúp phát hiện lỗi sớm, tiết kiệm chi phí sửa chữa sai lầm.
- Thúc đẩy văn hóa học hỏi và cải tiến liên tục: Nhân viên được khuyến khích thử nghiệm, học hỏi từ sai lầm và không ngừng cải tiến.
Như Tiến sĩ W. Edwards Deming từng nói:
“Without data, you’re just another person with an opinion.”
(Không có dữ liệu, bạn chỉ là một người có ý kiến chủ quan) [4].
PDCA chính là công cụ giúp bạn biến dữ liệu thành những cải tiến thực tế, từ đó nâng cao chất lượng, tối ưu hóa quy trình và đạt được thành công bền vững.
2. Kanban – Quản lý dòng công việc hiệu quả
Trong một thế giới mà tốc độ và hiệu suất quyết định sự thành công, Kanban đã trở thành một trong những phương pháp quản lý công việc phổ biến nhất. Kanban không chỉ giúp tối ưu hóa quy trình làm việc mà còn mang lại sự linh hoạt, giảm thiểu lãng phí và cải thiện hiệu suất tổng thể.
Như Peter Drucker đã từng nói:
“Efficiency is doing things right; effectiveness is doing the right things.”
(Hiệu suất là làm đúng việc; hiệu quả là làm những việc đúng) [4].
Kanban giúp tổ chức và cá nhân không chỉ làm việc hiệu quả hơn mà còn tập trung vào những nhiệm vụ quan trọng nhất, từ đó tạo ra giá trị tối ưu.
Nguồn gốc và nguyên tắc của Kanban
Kanban (tiếng Nhật có nghĩa là “biển hiệu” hoặc “bảng thông báo”) có nguồn gốc từ Toyota Production System (TPS)vào những năm 1940. Toyota sử dụng phương pháp này để tối ưu hóa chuỗi cung ứng, kiểm soát hàng tồn kho và đảm bảo dòng chảy công việc trơn tru.
Ngày nay, Kanban đã trở thành một công cụ quản lý linh hoạt, được áp dụng rộng rãi trong phát triển phần mềm, quản lý dự án, vận hành doanh nghiệp và cải thiện hiệu suất cá nhân.
Kanban hoạt động dựa trên ba nguyên tắc cốt lõi:
- Trực quan hóa công việc:
- Sử dụng bảng Kanban (Kanban board) để hiển thị tiến trình công việc.
- Các nhiệm vụ được thể hiện bằng thẻ (cards) di chuyển qua các cột trạng thái như “Việc cần làm” (To Do), “Đang thực hiện” (In Progress), và “Hoàn thành” (Done).
- Giới hạn công việc đang xử lý (WIP – Work In Progress):
- Hạn chế số lượng công việc đang thực hiện để tránh quá tải.
- Đảm bảo rằng nhóm chỉ tập trung vào những nhiệm vụ quan trọng nhất thay vì dàn trải nguồn lực.
- Tối ưu hóa dòng công việc (Flow Optimization):
- Loại bỏ các nút thắt trong quy trình.
- Sử dụng dữ liệu để phân tích hiệu suất và điều chỉnh chiến lược làm việc.
Ứng dụng của Kanban
Kanban có thể áp dụng trong nhiều lĩnh vực khác nhau:
- Phát triển phần mềm Agile:
- Các nhóm Agile sử dụng Kanban để theo dõi tiến độ phát triển sản phẩm, từ lập kế hoạch đến triển khai.
- Kết hợp với Scrum để tăng tính linh hoạt và khả năng thích nghi với thay đổi.
- Quản lý dự án:
- Giúp các đội nhóm theo dõi công việc, ưu tiên nhiệm vụ quan trọng và tối ưu hóa tiến độ dự án.
- Được sử dụng trong các công ty công nghệ, tài chính, marketing và sản xuất.
- Quản lý công việc cá nhân:
- Áp dụng Kanban trong việc tổ chức lịch làm việc, kiểm soát khối lượng công việc và nâng cao hiệu suất cá nhân.
- Các ứng dụng như Trello, Jira, Asana và ClickUp cho phép sử dụng Kanban để quản lý nhiệm vụ hàng ngày.
Ví dụ thực tế về Kanban
Microsoft – Quản lý quy trình phát triển phần mềm
Microsoft áp dụng Kanban trong nhóm phát triển phần mềm của họ để tối ưu hóa tiến trình làm việc, rút ngắn thời gian phản hồi và cải thiện chất lượng sản phẩm. Nhờ Kanban, nhóm phát triển có thể xác định nút thắt trong quy trình, giúp họ triển khai phần mềm nhanh hơn mà vẫn đảm bảo chất lượng.
Spotify – Điều phối đội nhóm sáng tạo
Spotify sử dụng Kanban để quản lý các chiến dịch marketing, phát triển tính năng mới và điều phối đội nhóm. Hệ thống Kanban giúp họ linh hoạt hơn trong việc triển khai các sáng kiến mới mà không bị gián đoạn bởi quy trình cứng nhắc.
Toyota – Tối ưu hóa chuỗi cung ứng
Toyota vẫn tiếp tục sử dụng Kanban để giảm thiểu lãng phí trong sản xuất, điều phối nguyên liệu một cách chính xác và đảm bảo sản phẩm đến tay khách hàng đúng thời điểm.
Tại sao Kanban hiệu quả?
- Giảm thiểu lãng phí: Giới hạn công việc đang xử lý giúp đội nhóm tập trung vào những nhiệm vụ có giá trị cao nhất.
- Tăng tính minh bạch: Mọi người trong nhóm đều có thể nhìn thấy trạng thái công việc, giúp cải thiện sự phối hợp.
- Thích nghi linh hoạt: Kanban không yêu cầu thay đổi toàn bộ quy trình, mà chỉ cần điều chỉnh để tối ưu hóa hiệu suất.
- Cải thiện hiệu suất cá nhân: Giúp cá nhân tổ chức công việc hiệu quả, tránh tình trạng làm nhiều việc cùng lúc mà không đạt hiệu suất cao.
Như Taiichi Ohno, cha đẻ của hệ thống sản xuất Toyota, từng nói:
“Something is wrong if workers do not look around each day, find things that are waste, and then do something about it.”
(Có điều gì đó sai nếu mỗi ngày, nhân viên không tìm kiếm những lãng phí và tìm cách loại bỏ chúng) [5].
Kanban chính là công cụ giúp các cá nhân và tổ chức nhận diện lãng phí, tối ưu hóa dòng công việc và nâng cao hiệu suất làm việc, từ đó tạo ra giá trị bền vững trong dài hạn.
3. 5S – Phương pháp tổ chức nơi làm việc
Trong một môi trường làm việc hiện đại, việc duy trì tính tổ chức, hiệu quả và sự gọn gàng đóng vai trò quan trọng trong nâng cao năng suất và chất lượng công việc. Phương pháp 5S xuất phát từ Nhật Bản đã chứng minh được hiệu quả trong việc tối ưu hóa không gian làm việc, loại bỏ lãng phí và nâng cao hiệu suất hoạt động của doanh nghiệp.
Như Benjamin Franklin từng nói:
“For every minute spent organizing, an hour is earned.”
(Mỗi phút dành cho việc tổ chức sẽ tiết kiệm được một giờ) [1].
Điều này cho thấy, một môi trường làm việc gọn gàng và khoa học không chỉ giúp tiết kiệm thời gian mà còn cải thiện đáng kể tinh thần làm việc và chất lượng đầu ra.
Nguồn gốc và nguyên lý của 5S
Hệ thống 5S có nguồn gốc từ Nhật Bản và được áp dụng rộng rãi trong Toyota Production System (TPS) nhằm tối ưu hóa quy trình sản xuất và nâng cao hiệu quả vận hành. Ngày nay, 5S không chỉ được sử dụng trong ngành sản xuất mà còn trong nhiều lĩnh vực như dịch vụ, công nghệ, y tế và quản lý văn phòng.
Phương pháp này bao gồm 5 bước chính, mỗi bước bắt đầu bằng chữ “S” trong tiếng Nhật:
- Seiri (整理) – Sàng lọc
- Loại bỏ những vật dụng không cần thiết khỏi nơi làm việc.
- Giữ lại những thứ có giá trị và sử dụng thường xuyên.
- Giảm thiểu tình trạng lộn xộn, giúp dễ dàng tìm kiếm tài liệu và công cụ.
- Seiton (整頓) – Sắp xếp
- Tổ chức không gian làm việc sao cho khoa học và thuận tiện.
- Sắp xếp dụng cụ, tài liệu, thiết bị theo một hệ thống hợp lý.
- Đảm bảo mọi vật dụng đều có vị trí cố định, giúp giảm thời gian tìm kiếm và tăng hiệu suất làm việc.
- Seiso (清掃) – Sạch sẽ
- Duy trì môi trường làm việc sạch sẽ, ngăn nắp.
- Loại bỏ bụi bẩn, rác thải, đảm bảo khu vực làm việc luôn trong trạng thái tốt nhất.
- Giúp phát hiện sớm các vấn đề về thiết bị, từ đó tránh gián đoạn hoạt động.
- Seiketsu (清潔) – Chuẩn hóa
- Thiết lập tiêu chuẩn để duy trì các bước trên.
- Xây dựng quy trình rõ ràng để đảm bảo mọi nhân viên tuân thủ nguyên tắc 5S.
- Tạo ra sự thống nhất trong tổ chức, giúp nâng cao hiệu suất làm việc.
- Shitsuke (躾) – Sẵn sàng
- Rèn luyện thói quen tuân thủ 5S như một phần văn hóa doanh nghiệp.
- Thường xuyên đánh giá, cải tiến để quy trình trở nên hiệu quả hơn.
- Khuyến khích nhân viên chủ động duy trì môi trường làm việc tối ưu.
Ứng dụng của 5S trong doanh nghiệp và cá nhân
5S không chỉ là một hệ thống quản lý trong doanh nghiệp, mà còn có thể áp dụng trong môi trường làm việc cá nhân để nâng cao năng suất.
- Trong sản xuất: Giúp giảm thời gian tìm kiếm công cụ, tối ưu hóa quy trình và giảm thiểu sai sót.
- Trong văn phòng: Hỗ trợ tổ chức tài liệu, email, không gian làm việc, giúp nhân viên làm việc hiệu quả hơn.
- Trong phát triển phần mềm: Giúp nhóm phát triển có quy trình làm việc rõ ràng, tránh dư thừa tài nguyên không cần thiết.
- Trong quản lý cá nhân: Ứng dụng 5S vào quản lý thời gian, sắp xếp công việc và tối ưu hóa lịch trình hàng ngày.
Lợi ích của phương pháp 5S
- Cải thiện năng suất: Nhân viên không phải lãng phí thời gian tìm kiếm tài liệu, công cụ làm việc.
- Giảm thiểu sai sót: Mọi thứ được tổ chức khoa học giúp công việc diễn ra trơn tru hơn.
- Nâng cao chất lượng công việc: Môi trường làm việc sạch sẽ, có tổ chức giúp cải thiện tư duy và sự tập trung.
- Tạo thói quen làm việc chuyên nghiệp: Khi 5S trở thành văn hóa doanh nghiệp, nhân viên sẽ có ý thức làm việc hiệu quả hơn.
Ví dụ thực tế về ứng dụng 5S
Toyota – Hoàn thiện quy trình sản xuất
Toyota đã áp dụng 5S như một phần quan trọng trong hệ thống quản lý sản xuất của họ, giúp họ giảm thiểu lãng phí, cải thiện quy trình làm việc và nâng cao chất lượng sản phẩm. Mỗi nhân viên tại Toyota đều được đào tạo về 5S để đảm bảo sự tuân thủ và tối ưu hóa sản xuất.
Google – Không gian làm việc sáng tạo
Google áp dụng nguyên tắc 5S trong tổ chức không gian làm việc, đảm bảo rằng mọi công cụ hỗ trợ sáng tạo đều được sắp xếp khoa học, giúp nhân viên có môi trường làm việc tốt nhất để phát huy tối đa ý tưởng của họ.
Môi trường văn phòng
Một công ty dịch vụ tài chính đã triển khai 5S trong việc quản lý tài liệu và email, giúp nhân viên tiết kiệm hàng trăm giờ mỗi năm chỉ bằng việc tổ chức lại hệ thống lưu trữ thông tin.
Tại sao 5S hiệu quả?
- Tăng cường kỷ luật: 5S giúp tạo thói quen làm việc có tổ chức, từ đó nâng cao tính kỷ luật trong tổ chức.
- Tiết kiệm thời gian: Một môi trường làm việc có tổ chức giúp nhân viên tập trung vào công việc thay vì lãng phí thời gian tìm kiếm tài liệu, công cụ.
- Tăng cường tinh thần làm việc nhóm: Khi mọi người cùng tuân thủ một hệ thống tổ chức, sự phối hợp giữa các phòng ban sẽ hiệu quả hơn.
- Cải thiện sự sáng tạo: Một không gian làm việc sạch sẽ, khoa học giúp tăng cường sự tập trung và thúc đẩy tư duy sáng tạo.
Như Taiichi Ohno, người sáng lập hệ thống sản xuất Toyota, đã từng nói:
“The more inventory a company has, the less likely they will have what they need.”
(Càng có nhiều hàng tồn kho, công ty càng ít có khả năng có đúng thứ họ cần) [2].
Hệ thống 5S không chỉ giúp tổ chức nơi làm việc khoa học, mà còn tạo ra một môi trường làm việc hiệu quả, chuyên nghiệp và bền vững.
4. Lean Manufacturing – Loại bỏ lãng phí
Trong môi trường kinh doanh đầy cạnh tranh, tối ưu hóa quy trình và giảm thiểu lãng phí là yếu tố quyết định sự thành công và bền vững của doanh nghiệp. Lean Manufacturing (sản xuất tinh gọn) không chỉ là một phương pháp quản lý sản xuất, mà còn là một triết lý giúp doanh nghiệp loại bỏ lãng phí, cải thiện hiệu suất và nâng cao giá trị cho khách hàng.
Như Shigeo Shingo, một trong những người tiên phong của hệ thống sản xuất Toyota, từng nói:
“The most dangerous kind of waste is the waste we do not recognize.”
(Loại lãng phí nguy hiểm nhất là loại mà chúng ta không nhận ra) [5].
Điều này nhấn mạnh tầm quan trọng của việc nhận diện và loại bỏ lãng phí, thay vì chấp nhận chúng như một phần tất yếu của quy trình.
Nguồn gốc và triết lý của Lean Manufacturing
Lean Manufacturing ra đời từ hệ thống sản xuất Toyota (Toyota Production System – TPS) và đã trở thành một mô hình tiêu chuẩn trong ngành công nghiệp toàn cầu. Mục tiêu của Lean là loại bỏ tất cả những gì không tạo ra giá trị cho khách hàng, từ đó giảm thiểu chi phí, nâng cao chất lượng sản phẩm và tối ưu hóa quy trình làm việc.
8 loại lãng phí trong Lean Manufacturing – TIMWOODS
Lean Manufacturing xác định 8 loại lãng phí (TIMWOODS), mà nếu không được kiểm soát, có thể làm giảm đáng kể hiệu suất và lợi nhuận của doanh nghiệp:
- Transportation (Vận chuyển)
- Di chuyển nguyên vật liệu, sản phẩm không cần thiết làm tăng chi phí và thời gian.
- Giải pháp: Sắp xếp bố trí kho hàng và dây chuyền sản xuất hợp lý để giảm thiểu quãng đường di chuyển.
- Inventory (Tồn kho)
- Hàng tồn kho dư thừa gây lãng phí không gian, tăng rủi ro hư hỏng, giảm dòng tiền lưu động.
- Giải pháp: Sử dụng mô hình sản xuất Just-In-Time (JIT) để duy trì mức tồn kho tối ưu.
- Motion (Di chuyển không cần thiết)
- Những thao tác không cần thiết của nhân viên như cúi, với, đi lại nhiều lần làm giảm hiệu suất làm việc.
- Giải pháp: Thiết kế lại không gian làm việc theo nguyên tắc 5S để tối ưu hóa quy trình thao tác.
- Waiting (Chờ đợi)
- Nhân viên hoặc máy móc bị gián đoạn do thiếu nguyên liệu, chậm trễ thông tin hoặc sự cố kỹ thuật.
- Giải pháp: Tối ưu hóa lịch trình sản xuất, cải tiến luồng công việc và tự động hóa các quy trình lặp đi lặp lại.
- Overproduction (Sản xuất thừa)
- Sản xuất nhiều hơn nhu cầu thực tế dẫn đến lãng phí nguyên liệu, lưu kho và nhân công.
- Giải pháp: Dự báo chính xác nhu cầu và sản xuất theo mô hình Pull System để giảm thiểu sản xuất dư thừa.
- Overprocessing (Xử lý thừa)
- Thực hiện các công đoạn không cần thiết, tạo ra chi phí mà không tăng giá trị cho khách hàng.
- Giải pháp: Đánh giá và đơn giản hóa quy trình sản xuất, loại bỏ những bước không tạo ra giá trị.
- Defects (Lỗi sản phẩm)
- Sản phẩm lỗi gây lãng phí nguyên vật liệu, thời gian sản xuất và chi phí sửa chữa.
- Giải pháp: Áp dụng kỹ thuật Poka-Yoke (chống sai sót), kiểm soát chất lượng từ đầu vào đến đầu ra.
- Skills (Lãng phí kỹ năng nhân sự)
- Không tận dụng tối đa năng lực của nhân viên, khiến họ không phát huy hết tiềm năng.
- Giải pháp: Đào tạo, luân chuyển công việc và tạo môi trường làm việc sáng tạo để tối ưu hóa nguồn lực.
Ứng dụng Lean Manufacturing trong doanh nghiệp
Lean không chỉ giới hạn trong ngành sản xuất mà còn có thể áp dụng trong dịch vụ, y tế, công nghệ và quản lý doanh nghiệp.
- Trong sản xuất: Loại bỏ lãng phí nguyên liệu, tối ưu hóa quy trình sản xuất và cải thiện chất lượng sản phẩm.
- Trong công nghệ: Áp dụng mô hình Lean Software Development để giảm thiểu lỗi phần mềm, rút ngắn thời gian phát triển.
- Trong chăm sóc sức khỏe: Tối ưu hóa quy trình khám chữa bệnh, giảm thời gian chờ đợi của bệnh nhân.
- Trong quản lý doanh nghiệp: Cải thiện quy trình nội bộ, tối ưu hóa nguồn lực và nâng cao hiệu suất đội nhóm.
Ví dụ thực tế về Lean Manufacturing
Toyota – Người tiên phong của Lean
Toyota đã áp dụng Lean Manufacturing vào quy trình sản xuất, giúp giảm chi phí vận hành, tối ưu hóa thời gian giao hàng và cải thiện chất lượng sản phẩm. Hệ thống Just-In-Time (JIT) của Toyota giúp giảm đáng kể hàng tồn kho và tăng hiệu suất sản xuất.
Amazon – Tinh gọn chuỗi cung ứng
Amazon sử dụng Lean để tối ưu hóa hệ thống logistics, giúp giao hàng nhanh chóng và giảm chi phí vận hành. Họ liên tục cải tiến hệ thống kho hàng tự động, đảm bảo hàng hóa luôn được sắp xếp khoa học và vận chuyển nhanh nhất có thể.
Tesla – Cải tiến liên tục trong sản xuất ô tô
Tesla áp dụng Lean Manufacturing và tự động hóa để tối ưu hóa dây chuyền sản xuất, giúp giảm chi phí sản xuất ô tô điện và tăng tốc độ sản xuất. Họ liên tục điều chỉnh quy trình để nâng cao chất lượng sản phẩm mà không lãng phí tài nguyên.
Lợi ích của Lean Manufacturing
- Giảm chi phí vận hành: Loại bỏ lãng phí giúp doanh nghiệp tiết kiệm nguồn lực và tăng lợi nhuận.
- Cải thiện chất lượng sản phẩm: Quy trình tối ưu giúp giảm lỗi, nâng cao độ tin cậy của sản phẩm.
- Tăng tốc độ sản xuất: Giúp doanh nghiệp nhanh chóng đáp ứng nhu cầu khách hàng.
- Nâng cao sự hài lòng của khách hàng: Sản phẩm chất lượng hơn, giá cả cạnh tranh hơn.
- Xây dựng môi trường làm việc tốt hơn: Nhân viên có cơ hội phát triển, làm việc hiệu quả hơn.
Như Taiichi Ohno, cha đẻ của Toyota Production System, từng nói:
“All we are doing is looking at the timeline from order to cash and reducing that timeline by removing the non-value-added wastes.”
(Tất cả những gì chúng tôi làm là xem xét dòng thời gian từ khi đặt hàng đến khi nhận tiền và rút ngắn nó bằng cách loại bỏ các lãng phí không tạo ra giá trị) [6].
Lean Manufacturing không chỉ là một phương pháp sản xuất, mà còn là một triết lý quản lý giúp tổ chức tối ưu hóa hiệu suất, cắt giảm lãng phí và phát triển bền vững.
III. Kết luận
Cải tiến liên tục không chỉ là một chiến lược, mà còn là một tư duy giúp cá nhân và tổ chức duy trì sự phát triển bền vững trong một thế giới không ngừng thay đổi. Những doanh nghiệp hàng đầu như Toyota, Amazon, Tesla, Google đều coi cải tiến liên tục là kim chỉ nam trong chiến lược vận hành của họ. Điều này giúp họ tối ưu hóa quy trình, giảm thiểu lãng phí, nâng cao chất lượng sản phẩm và cải thiện trải nghiệm khách hàng.
Như Steve Jobs từng nói:
“Innovation distinguishes between a leader and a follower.”
(Đổi mới là thứ phân biệt giữa một nhà lãnh đạo và một người đi theo) [6].
Việc áp dụng các phương pháp như PDCA, Kanban, 5S, Lean Manufacturing không chỉ giúp doanh nghiệp nâng cao năng suất mà còn tạo ra giá trị bền vững, tăng tính cạnh tranh và đảm bảo sự thành công lâu dài.
Bài học từ những doanh nghiệp thành công
- Toyota áp dụng Lean Manufacturing, giúp loại bỏ lãng phí và tối ưu hóa sản xuất, đưa họ trở thành hãng xe hơi hàng đầu thế giới.
- Amazon sử dụng Kanban và cải tiến chuỗi cung ứng, giúp giao hàng nhanh chóng, tối ưu hóa chi phí và nâng cao trải nghiệm khách hàng.
- Tesla liên tục đổi mới bằng cách kết hợp Lean, tự động hóa và dữ liệu lớn, giúp rút ngắn thời gian sản xuất xe điện mà vẫn đảm bảo chất lượng cao.
- Google áp dụng PDCA và văn hóa thử nghiệm, giúp họ luôn đi đầu trong đổi mới công nghệ và cải tiến sản phẩm.
Tư duy cải tiến liên tục – Yếu tố sống còn trong thời đại mới
Trong một thế giới mà công nghệ, thị trường và hành vi khách hàng thay đổi từng ngày, những cá nhân và tổ chức không sẵn sàng cải tiến sẽ nhanh chóng bị bỏ lại phía sau. Để duy trì lợi thế cạnh tranh, mỗi doanh nghiệp, đội nhóm và cá nhân cần liên tục học hỏi, đổi mới và cải tiến từng ngày.
Làm thế nào để bắt đầu?
- Đưa cải tiến liên tục vào văn hóa tổ chức: Tạo môi trường khuyến khích đổi mới, phản hồi và thử nghiệm.
- Sử dụng dữ liệu để ra quyết định: Thu thập và phân tích dữ liệu để tối ưu hóa quy trình.
- Đào tạo và phát triển nhân sự: Cung cấp công cụ và kiến thức giúp đội ngũ thích nghi với những thay đổi.
- Ứng dụng các phương pháp đã được chứng minh: PDCA, Kanban, 5S, Lean giúp tối ưu hóa hiệu suất và loại bỏ lãng phí.
- Đánh giá và cải thiện liên tục: Định kỳ xem xét các quy trình và tìm cách tối ưu hóa tốt hơn.
Cải tiến liên tục không phải là một đích đến, mà là một hành trình không ngừng tiến lên. Hãy áp dụng ngay từ hôm nay để nâng cao hiệu suất cá nhân, tối ưu hóa quy trình doanh nghiệp và tạo ra giá trị bền vững cho tương lai.
IV. Tài liệu tham khảo
[1] B. Franklin, Autobiography of Benjamin Franklin. Boston, MA: Houghton Mifflin, 1909.
[2] C. Darwin, On the Origin of Species. London, UK: John Murray, 1859.
[3] J. Ruskin, The Seven Lamps of Architecture. Smith, Elder & Co., 1849.
[4] P. Drucker, The Effective Executive. HarperBusiness, 1967.
[5] S. Shingo, A Study of the Toyota Production System. Productivity Press, 1989.
[6] S. Jobs, Speech at Stanford University, 2005.
Nguồn: SmartSkills – Người viết: Đặng Thanh Tùng